Vibration monitoring is the process of monitoring machinery to identify vibrations which may indicate a developing failure, malfunction, or process restriction. It is a major component of predictive maintenance. Properly monitoring critical equipment can prevent unscheduled outages, optimize machine performance, and reduce repair and maintenance costs.
Vibration monitoring primarily applies to machinery that rotates such as pumps, motors, turbines, fans and compressors. As seen in the chart below, the first sign of the impending failure of rotational equipment is vibration. By installing vibration detection equipment such as alignment sensors or seismic sensors, users can establish a baseline value and monitor for variations from that baseline. If anomalies are detected, steps can be taken prior to failure of the equipment.
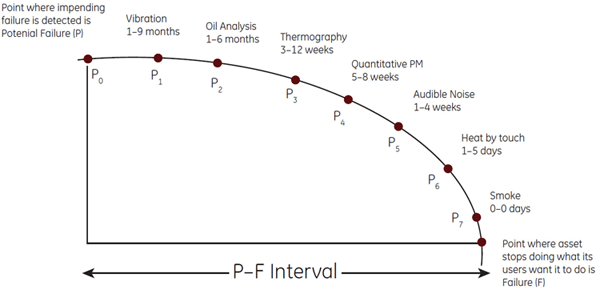
Benefits of Vibration Monitoring:
- Reducing maintenance and production costs
- Complying with environmental and safety regulations
- Preventing environmental releases
- Minimizing unplanned outages and downtime
- Extending the time between and reducing the duration of planned outages
- Life Cycle Asset Management – optimizing maintenance and operating costs to maximize the useful life of your production and assets
- Protecting critical machinery against catastrophic mechanical failures
- Reducing workforce size - reducing unnecessary maintenance and optimizing planned maintenance based on condition monitoring
- Improved Process Knowledge
Resources:
Bently Nevada Asset Management 101 Handbook
If you have any questions regarding vibration monitoring please don't hesitate to speak with one of our engineers by e-mailing us at sales@instrumart.com or calling 1-800-884-4967.